What is Integral Skin Foam?
Integral skin foam, also known as self-skinning foam or semi-rigid foam, is a type of polyurethane foam that has a dense, durable outer layer and a lightweight, porous inner core. It is called “integral skin” because the skin or outer layer is formed integrally with the foam during the manufacturing process.
The manufacturing of integral skin foam involves the use of a specialized foam dispensing machine. The machine combines two liquid components: a polyol (polyester or polyether) and an isocyanate. These components react chemically to form a foam that expands and solidifies into a cellular structure.
In the case of integral skin foam, a special formulation is used that allows the outer layer to have a higher density and a different chemical composition compared to the inner core. The outer layer typically has a compact, smooth, and tough surface, while the inner core is lightweight and porous, providing insulation and cushioning properties.
The skin of integral skin foam is created by a chemical reaction that occurs when the foam is dispensed into a mold or shaped using a spray gun. The reaction causes the outer layer of the foam to skin over and form a solid, durable surface. This outer skin is resistant to abrasion, impact, chemicals, and UV radiation, making it suitable for a wide range of applications.
Integral skin foam is commonly used in the production of furniture, automotive components, medical equipment, and sporting goods. It is often employed in applications where a combination of comfort, durability, and aesthetics is desired. For example, it can be found in car seats, armrests, steering wheels, and headrests, providing a comfortable and visually appealing surface while offering resistance to wear and tear.
Integral skin foam, also commonly referred to as “self-skinning” foam, is a dual-layer structure formed through a material’s foaming process. This composition, similar to a loaf of bread, features a foam inner core surrounded by a solid outer crust or “skin”. While several materials can be used to produce an integral skin foam, thermoset polyurethanes can offer customizable properties to meet exact design requirements, including density, hardnesses, tensile strength, chemical resistance, and many more. Due to its adaptability, polyurethane integral skin foams can be manufactured through a cast or Reaction Injection Molding (RIM) process.
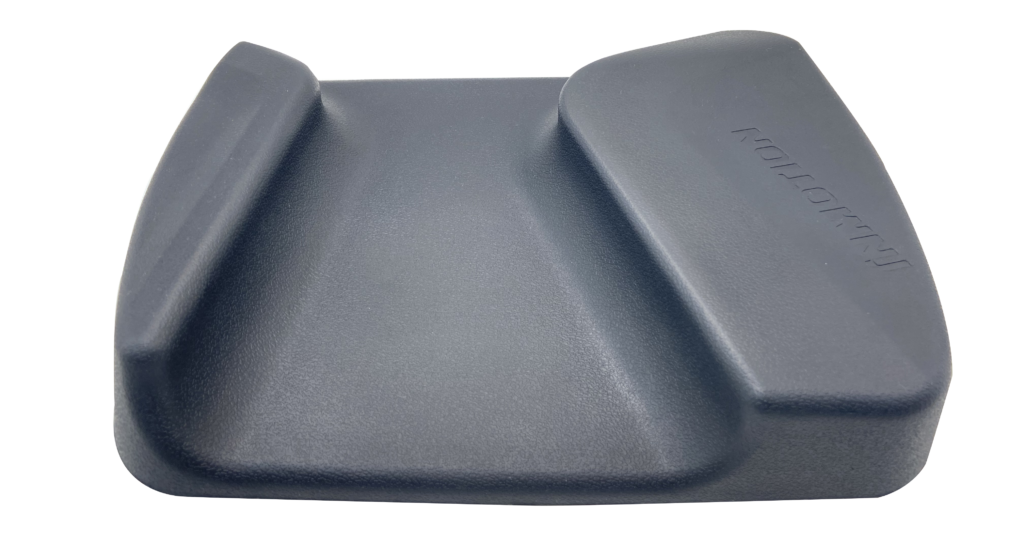
Benefits of Integral Skin Foam
There are 3 key things to consider in your product design when determining if integral skin foam is appropriate for your application, such as:
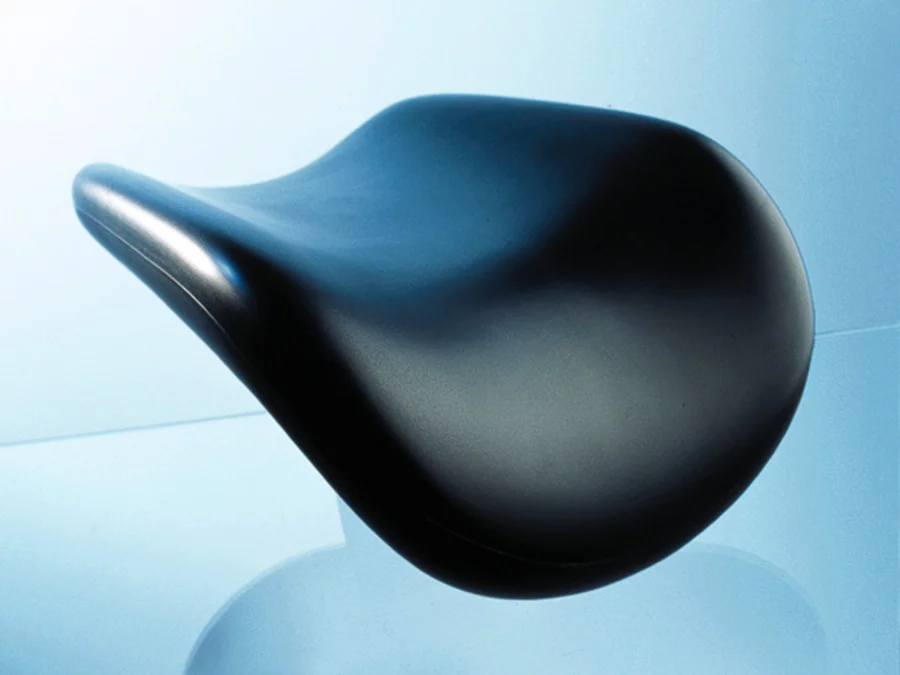
Aesthetics
Integral skin foams can display a uniform surface that portrays either a smooth or textured finish. Because of this, product designers can eliminate painting or other secondary operations to achieve a nice aesthetic.
Performance
Integral skin foams can provide a different set of physical properties than the foam layer underneath. For example, the Coefficient of Friction (COF) of foam with an integral skin will be higher due to its smooth, shiny surface, while the exposed foam may portray a lower COF.
Non Porous
Integral skin foams can prevent any air, dust particles, or liquids from flowing through, creating a non-breathable material. Although closed-cell foams can be achieved without a skin, there is still some level of porosity left behind. To ensure the porosity of the cellular structure is completely closed, an integral skin may be recommended.
How to use Integral Skin Foam in Your Design
Integral skin foams can virtually be found anywhere that benefits from its physical properties. This is often determined by the product’s overall function or purpose for optimal performance. For instance, products such as structural foam enclosures for robotics or elastomeric foam cushioning for fitness equipment may benefit from an integral skin due to its customizable aesthetics and superior properties. Whereas, products found in high-speed paper & media applications, such as foam rollers or belts, may exhibit poor COF and increased wear with an integral skin. While this material can offer a diverse set of capabilities, integral skin foams can also portray a negative effect on your product’s performance if not used appropriately.
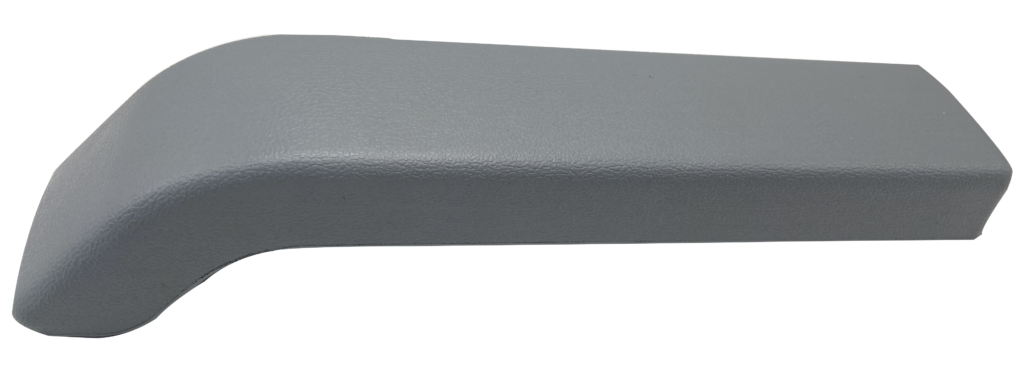
Conclusion
Overall, integral skin foam is a versatile material that combines the lightweight and cushioning properties of foam with a durable and attractive outer skin. Its unique characteristics make it well-suited for various applications in industries where comfort, impact resistance, and aesthetic appeal are essential.
Integral skin foams may be a key material for products and components that require a particular aesthetic or performance. As you further explore if integral skin foams are appropriate for your product design, it is important to consider your parts function, aesthetics, and physical property requirements beforehand. If you are still uncertain if integral skin foams are appropriate for your product design, Please email me. johnxiao@smpufoam.com