About Us
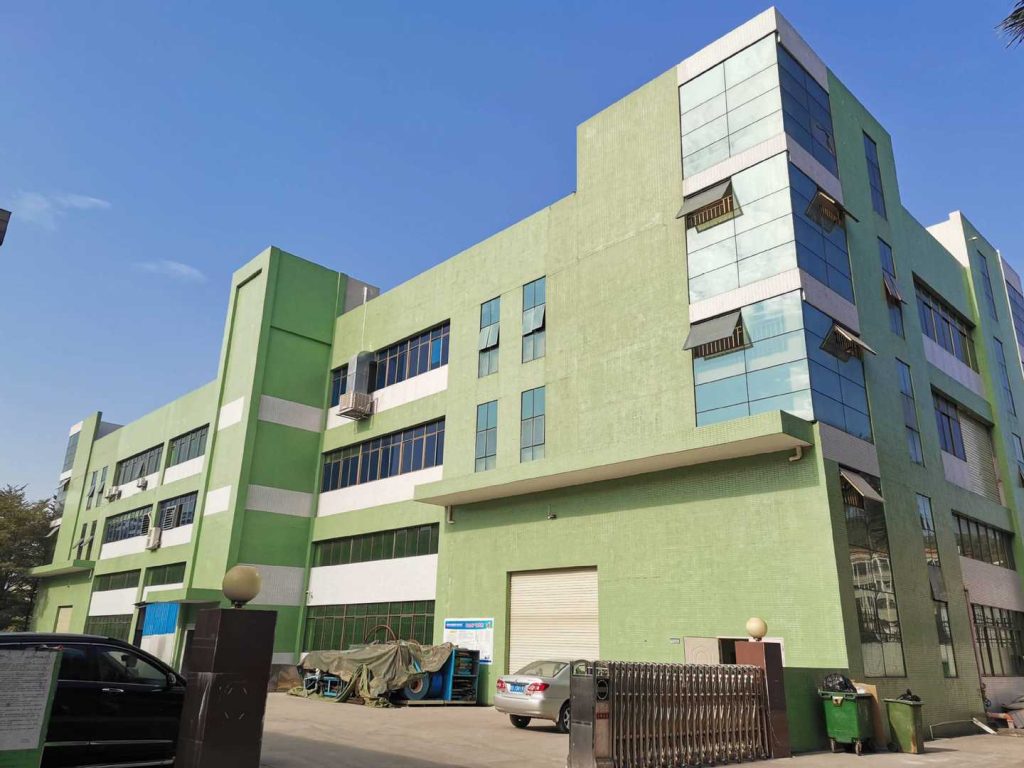
SMPUFOAM Polyurethane Foam Products Manufacturer
We Are Trusted by More Than 250+ Clients
SMPUFOAM is a of polyurethane foam products manufacturer with 25 years experience, Has a 25+ years of experience in foam technology, we produce highly engineered polyurethane molded parts for a variety of industrial markets including self-skinning and small pour molded polyurethane components for medical, pillows, cushions, footwear, impact protection, sporting goods and toys.
Customize various polyurethane product services.

25
Years of Experience
Why Choose Us?
Focus On Getting Our Jobs Done Quickly
SMPUFOAM is a of polyurethane foam products manufacturer with 25 years experience.
Focus on the research and innovation of Molded Polyurethane Materials.
- Unmatched performance, satisfaction service guarantees
- Upfront, flat rate pricing—no overtime charges
- 24 / 7 availability for all emergency services
- Fixed right promise—done right or it’s free
- Clear communication and updates on service arrival
Certification
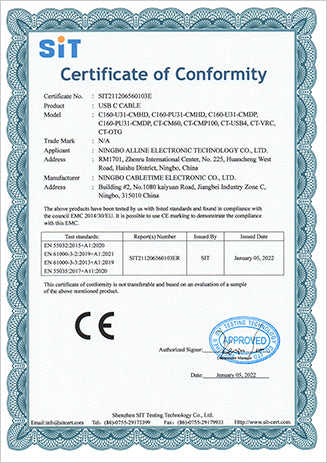
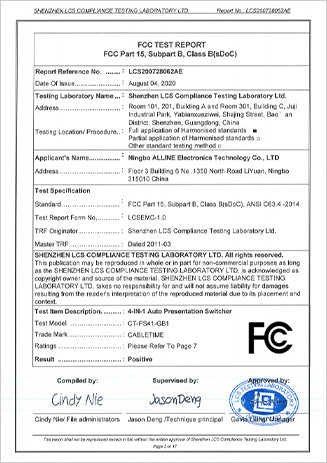
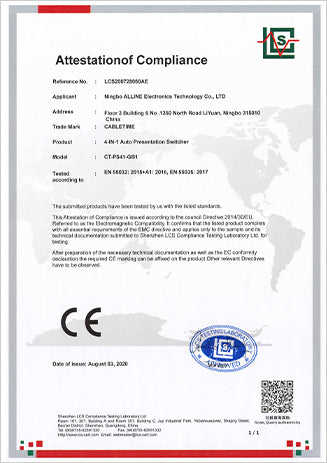
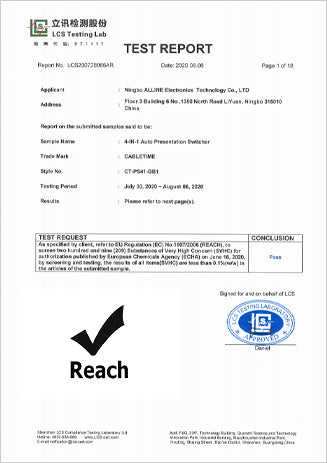
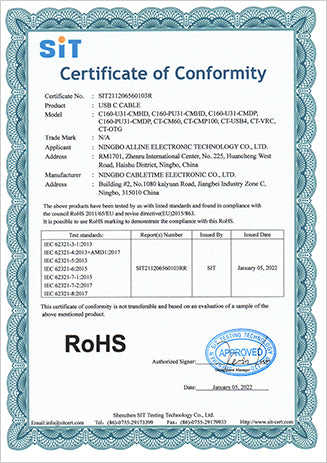
Polyurethane is a plastic material with changing characteristics and very diversified fields of application. Its discovery took place in Germany between the 1920s and the 1940s, but only from the following decade was it patented and developed as an industrial production process. In its basic formulation it is formed by the reaction between two main basic components (Di-Isocyanate and Polyol) but, depending on the different composition of the base elements and / or the addition of different additives, it can take on physical characteristics, resistance, or surface finish that make it specific and suitable for numerous uses in commodity sectors extremely wide and differentiated.
We can obtain types of soft or flexible polyurethane, or rigid with variations on the type of surface finish. Polyurethane is an excellent thermoacoustic insulation as well as an alternative to plastic components obtained with injection molding technology. It is suitable for food use and is environmentally friendly and recyclable.
It is the material typically used to make padding or protective cases for delicate parts. Classic examples of use can be found in the automotive sector as upholstery for seats or in the field of upholstery for sofas, armchairs, cushions and mattresses. It does not have its own surface finish so it is usually coated to obtain the final aesthetic surface.
It is a formulation that allows to obtain a product with elastic characteristics and softness typical of a padding but with an excellent aesthetic surface finish, eliminating in fact the need to cover the product with other materials and can be printed with different colors. The external surface can further be customized to the mold, with the possibility of obtaining a smooth, satin finish, embossed or with specific designs. You can find this type of applications in the automotive, furniture, medical, agricultural, toys and consumer products sectors.
This product and this technology (Reaction Injection Molding) allow to obtain details very similar to plastic products obtained by injection molding, advantageous compared to these for the lower cost of the mold and for the possibility of creating even large parts. We can find examples of applications in the automotive sector such as bumpers, bonnets, panels or interior parts. This material, resistant and pleasant to the touch, can have an aesthetic surface finish that can be molded or easily painted.
This type of polyurethane is typically used as a thermal-acoustic insulation, insulating panels, thermal insulation for refrigeration or boiler systems.
One of the most obvious advantages of polyurethane is its versatility. It is a material that, by varying the formulation of the components, can take on very different physical characteristics, allowing in any case a freedom to design the product almost without limits.
It is an economic chain material, the molds and the equipment necessary to realize the project are basically much simpler than a plastic injection mold. The relationship between quality and durability makes it one of the most competitive and innovative materials compared to other raw materials. Polyurethane is increasingly used in multi-sector applications such as automotive, earth-moving, logistics and handling, furniture, toys, medical, design and industry. It also offers the possibility to imagine and create the most complex and complex forms of design.
Polyurethane can cover different sectors of use and types of use.
In order to obtain the best results, it is necessary to combine the characteristics of the material with the correct molding equipment and the most suitable production process.
For this reason there are different types of molds that differ mainly due to the material with which they are made.
It is possible to co-print, together with the polyurethane, structural elements and fixing accessories or simply mount them in the mold before carrying out the casting process.
It is an ecological and safe product. The current chemical and process compositions of polyurethane products do not use aggressive solvents and do not use CFC11 or HCFC giving rise to an inert product. The use of this material as thermal insulation contributes to energy savings and therefore to a positive impact on the environment.
Polyurethane is a recyclable material and some of its formulations have obtained approval as a food product.
Frequently Asked Question From Clients
One of the most obvious advantages of polyurethane is its versatility. It is a material that, by varying the formulation of the components, can take on very different physical characteristics, allowing in any case a freedom to design the product almost without limits.