Rigid integral skin foam High strength – low weight
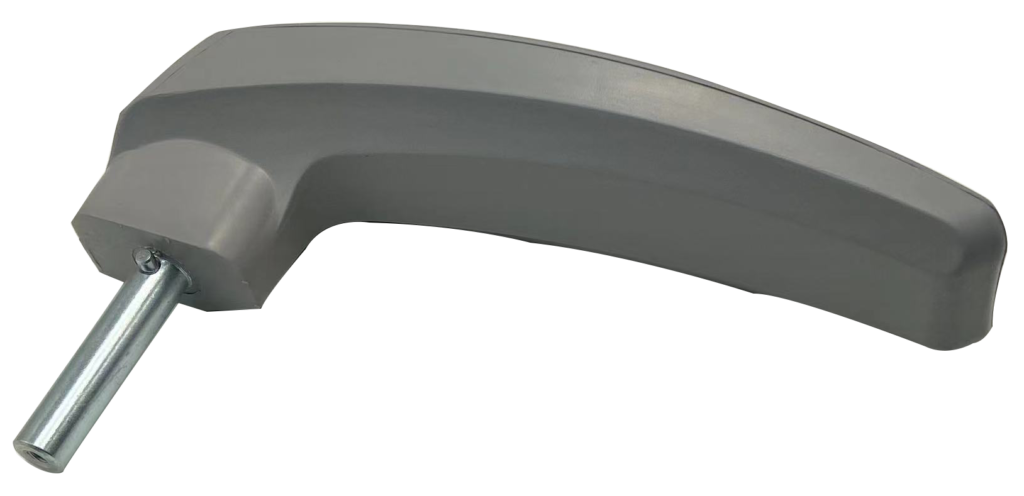
Rigid integral skin foam. High strength, low weight polyurethane foam is a type of foam material that offers excellent strength and durability while maintaining a low overall weight. Polyurethane foam is a versatile material widely used in various industries, including construction, automotive, aerospace, and marine applications, due to its desirable properties such as thermal insulation, cushioning, and impact resistance.
To achieve high strength and low weight characteristics, certain modifications can be made to the formulation and production process of polyurethane foam. Here are a few factors that contribute to achieving this balance:
- Density: The density of the foam can be controlled to achieve the desired strength-to-weight ratio. By adjusting the amount of blowing agents or additives, manufacturers can produce foams with lower densities, resulting in reduced weight while still maintaining structural integrity.
- Cellular Structure: Polyurethane foam consists of a network of interconnected cells. The size and distribution of these cells play a crucial role in determining the foam’s strength and weight. By optimizing the foam formulation and controlling the expansion process, smaller and more uniform cells can be achieved, resulting in improved strength and reduced weight.
- Reinforcement: In some cases, reinforcing materials such as fibers, fabrics, or structural additives can be incorporated into the foam matrix to enhance its mechanical properties. These reinforcements can improve the foam’s strength and stiffness without significantly increasing its weight.
- Chemical Formulation: The selection of specific polyols, isocyanates, and other additives used in the foam formulation can influence the final material properties. By carefully choosing the constituents and their proportions, manufacturers can optimize the foam for high strength while keeping the weight to a minimum.
The resulting high strength, low weight polyurethane foam can be used in a range of applications. For example, it can be utilized in lightweight composite structures for aerospace components, energy-absorbing panels in automotive applications, buoyancy materials for marine use, or as core materials in sandwich structures for building and construction.
It’s important to note that the specific properties and formulations of high strength, low weight polyurethane foam can vary depending on the desired application and requirements. Manufacturers often tailor the foam’s characteristics to meet the specific needs of their intended use.
Rigid integral skin foam. you can produce components with sandwich material structure in one step. The reaction mixture foams in the closed mould: Due to specific compression and temperature ratio it produces a foam core with fine pores and a massive edge zone. Density is integrally distributed in the component’s cross-section.
Depending on density, hardness adjustment and degree of compression different material properties can be achieved. This provides products from lightweight construction to structure functions to high-quality class A surfaces. Completely according to your requirements.
Applications
Trim parts / housings / covers
High-quality heat-insulating energy-saving windows with high stiffness
Clamps and pipe supports
Decor and furniture elements (stable in shape and extra light) for caravans and other camping cars
construction bars
SMPUFOAM
Has a 25+ years of experience in polyurethane foam products technology, we produce highly engineered polyurethane molded parts for a variety of industrial markets including self-skinning and small pour molded polyurethane components, medical, pillows, cushions, footwear, impact protection, sporting goods and toys.
One of the most obvious advantages of polyurethane is its versatility. It is a material that, by varying the formulation of the components, can take on very different physical characteristics, allowing in any case a freedom to design the polyurethane foam products almost without limits.